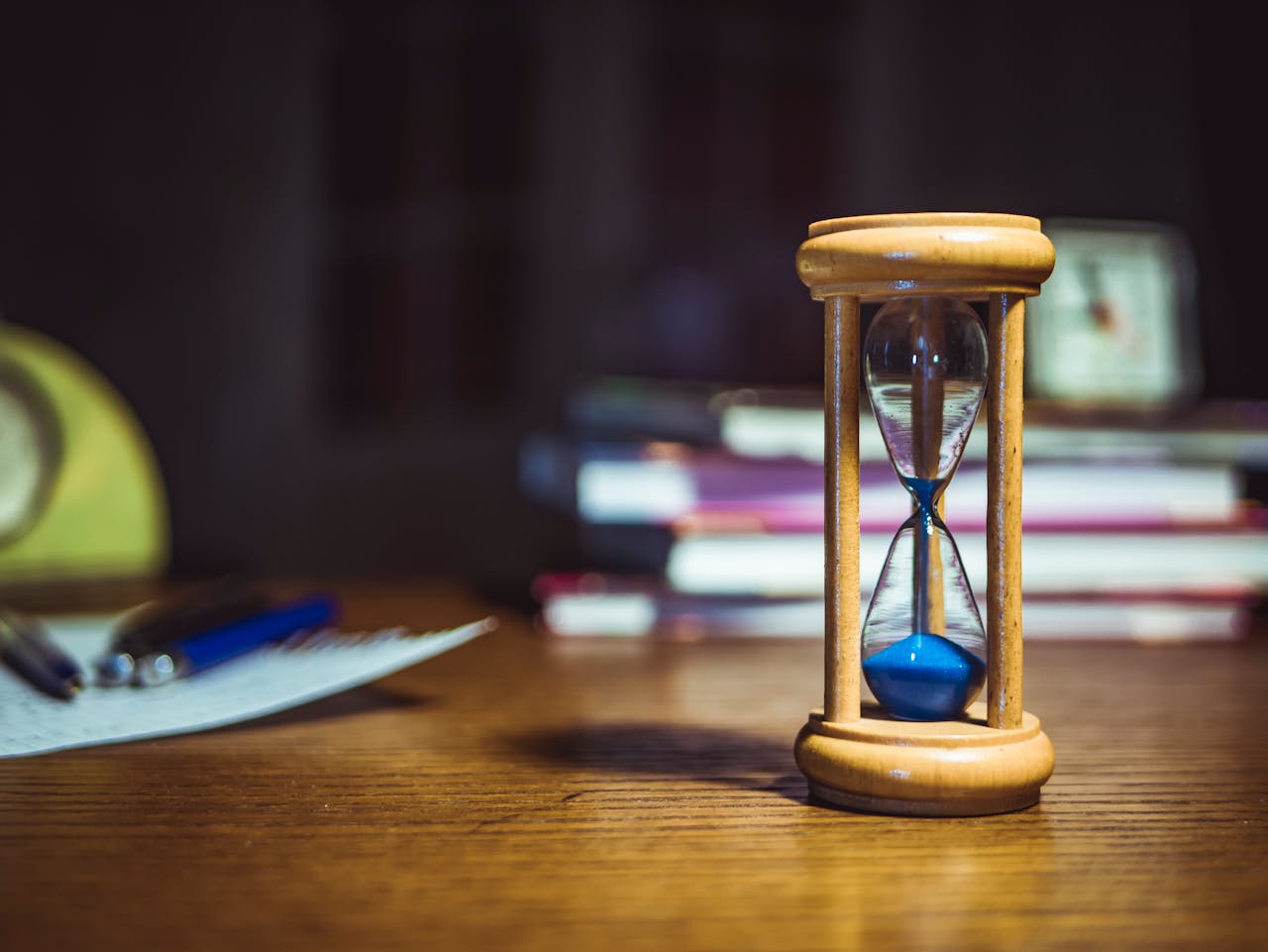
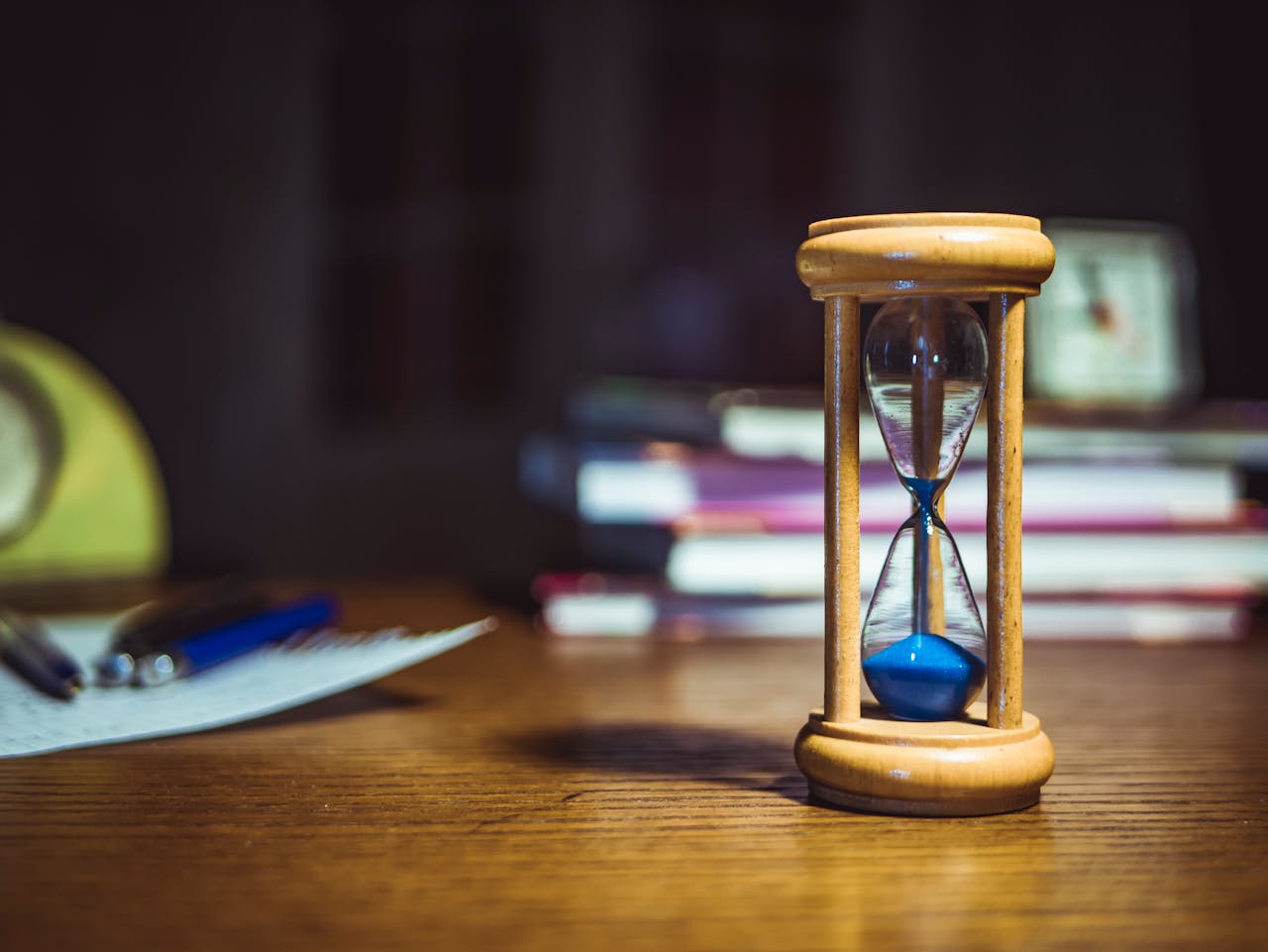
Cutting time waste is crucial, especially for industries in which efficiency is paramount for long-term success. If you don’t have control over how much time you and your employees are spending on routine tasks, your operations and profitability are going to suffer.
But how exactly are you supposed to track down areas of time waste? And what are the best strategies for eliminating them?
The Low-Hanging Fruit of Time Waste
In business, saving time is saving money. On a broad scale, it’s easy to see how receiving weeks or days of time can benefit your organization, accelerating your output and allowing you to serve more customers faster. But even on the narrowest scales, time savings can add up to massively benefit your organization.
Saving even a few minutes on an activity repeated hundreds or thousands of times can add up to dozens or hundreds of hours of time savings. In many cases, this can save you money directly by reducing your need for labor or peripheral services, and in all cases, the accelerated timeline puts you in a more competitive position.
The High-Level Vision for Eliminating Time Waste in Business
From a high level, you can use many strategies and techniques to evaluate and act on findings of time waste. For example:
Process Engineering
Process engineering is one of your best tools for eliminating time waste. In other words, process engineering is a collection of different practices designed to examine the layout and processes of your organization as critically as possible, identifying points of inefficiency and weaknesses that can be corrected for some material benefit. With the help of experienced process engineers, you can pinpoint some of the most egregious areas of time waste in your business so you can correct them.
Internal Audits
It’s a good idea to conduct internal audits to closely examine your internal systems and processes for potential improvements. Your leaders and team members are intimately familiar with how things work here, so they should be in a position to effectively speculate about ways to streamline things.
Consulting
In many cases, it pays to work with external consultants as well. Although your team members will be more intimately familiar with your business and its processes, a team of expert consultants will have neutral, third-party perspectives that can compensate for your blind spots and biases.
In any case, you’ll follow a process similar to the following:
Data Gathering
Everything starts by conducting an analysis of your business and its systems as they currently exist. You should gather as much information as possible, whether you’re focusing on the organization as a whole or some specific department or component of your organization. This includes not only objective information but also subjective reports from your team members.
Review
Once you have all the data in front of you, you can review it and systematically determine your weak points. There will probably be at least a few obvious improvements that can be made, but you’ll need to dig deeper if you want to eliminate less apparent instances of time waste.
Recommendations
After the analysis, the point person in charge of ameliorating time waste should make a list of concrete recommendations. Reorchestrating infrastructure, redesigning processes, and imposing new policies and rules can all play a role in making your organization more efficient and streamlined.
Deployment
Once these recommendations have been reviewed and approved, you can begin deploying them. The process doesn’t end here; not all of your recommendations are going to be as effective as you imagined, and it’s likely that you missed a few key considerations during your deliberations. This is your opportunity to conduct a live experiment and determine which changes are going to be most effective.
Analysis
When this test period is over, you should reflect on the changes you’ve made, analyze how much of an impact they’ve had, and create a new list of recommendations for modifying your previous recommendations or instituting further changes.
Areas to Consider When Eliminating Time Waste
During the course of your analysis, consider the following:
High-level Institutional Design
How is your facility and its internal departments laid out? What kinds of networks and systems are used to keep your organization running?
Production
What are your production and delivery processes like? What are the steps that need to be followed, how are they followed, and what complications can interfere with your ability to produce things efficiently?
Supply Chain
The integrity and efficiency of your supply chain has a major impact on the overall productivity of many organizations. What types of relationships do you have with your suppliers, and how could those relationships be improved to streamline productivity on your end?
Customer Relationships
Similarly, what types of relationships do you have with your customers? How can you expedite your dealings with them?
You can apply changes in areas like:
Infrastructure
Improving your equipment, devices, procedures for utilizing your equipment, and the layout of your equipment can all greatly improve your ability to spend time efficiently. Investing in a more advanced machine or rearranging your layout can save a lot of time.
Processes
Chances are, you already have some processes that allow your company to remain operational and profitable. But are these processes as streamlined as they should be? Are there any unnecessary or redundant steps that can be eliminated?
Internal Systems and Tools
What kinds of technologies, systems, and tools do your employees use to do their jobs effectively? Can they be improved? Are they causing time waste in hidden, unexpected ways?
The Human Element
And, of course, you need to think about the people within your organization. Are you hiring the best candidates? Do they have the education and training necessary to do their jobs effectively? Is there proper supervision or oversight to encourage more productive actions? Or is there an excess of supervision or oversight bogging things down?
The Most Common Areas of Time Waste
If you’re looking for places to get started, these are some of the most common areas of time waste in business:
Wait Times and Bottlenecks
Bottlenecks of any kind in your business can lead to excessive wait times, significantly slowing down your operation. These types of bottlenecks can occur for many different reasons, such as broken machines, flawed internal processes, long wait times for raw materials, or general infrastructural issues. In any case, your team members shouldn’t be waiting around for something to do.
Transportation
Improper transportation management can cost you days, or even weeks of time. For example, if your supply chain isn’t effective, or if you have shipping and logistical issues, it can stop you from being able to move materials freely.
Movement
On a smaller scale for physical businesses, you’ll need to think about how people and equipment move within your facility. How much time does it take to get from point A to point B in your facility? Also, how are you tracking and measuring movement time? And, how can you shorten these distances?
Redundant/Unnecessary Processing
How many process steps are truly necessary in the way you currently do things? In most businesses, leaders can streamline processes by simplifying the order of operations and cutting out unnecessary review steps. Supervision and oversight are necessary for quality assurance and other reasons, but these actions need to be deliberate and executed efficiently if you want your organization to run smoothly.
Inventory Problems
Various inventory problems can slow down your operations as well. For instance, if you don’t have the materials or information you need, you won’t be able to produce things effectively. If you have a surplus of inventory, you’ll run into storage issues that complicate your productive operations.
Defects and Mistakes
Errors in the process, which can be attributable to equipment failures, human mistakes, and myriad other factors, also present complications. If you want to save time, you need to employ proactive measures to prevent and mitigate defects and mistakes. You’ll need to be careful to strike the right balance here; proactively expending effort to prevent a mistake can be a good investment, but if you go overboard, this can turn into a waste of time in its own right.
Labor Issues
Businesses sometimes waste time globally because the individuals executing the work aren’t working as efficiently as they could be. This manifests in a wide variety of potential applications, from workers who waste time on unnecessary procedures because of unclear instructions to workers who spend too much idle time because they aren’t properly motivated to do their jobs. The range of solutions for labor issues is as diverse as the labor issues themselves. Potential fixes include things like better education, better training, more supervision, superior causes for motivation, and more.
There’s no such thing as a perfectly efficient organization. No matter how many analyses you conduct or how many recommendations you put to good use, there are going to be instances of time waste within your business. What’s important is that you adopt a mentality of productivity and continuous improvement so you can gradually inch closer to an efficient ideal – and hopefully get an edge on your competitors in the process.
Featured Image Credit: Photo by Mike; Pexels; Thank you.
Deanna Ritchie
Editor-in-Chief at Calendar. Former Editor-in-Chief and writer at Startup Grind. Freelance editor at Entrepreneur.com. Deanna loves to help build startups, and guide them to discover the business value of their online content and social media marketing.